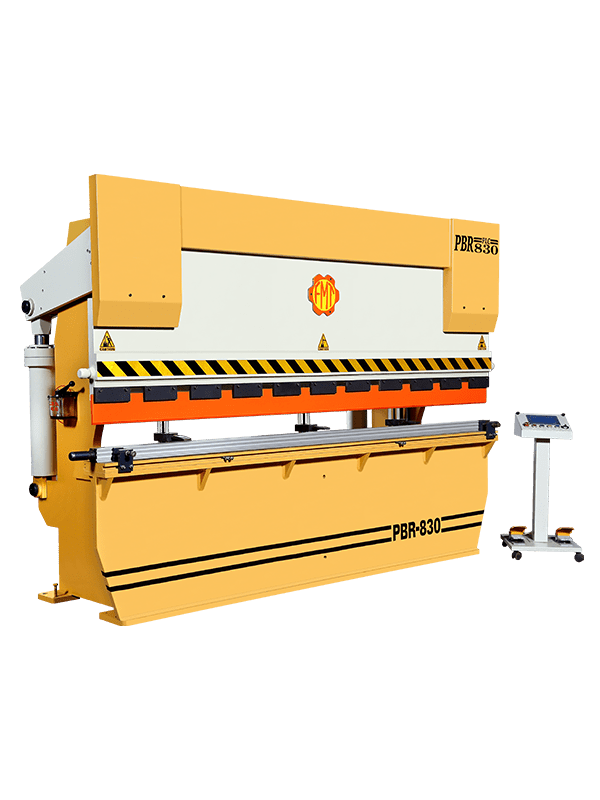
What is Press Brake? How does the press brake work?
November 1, 2021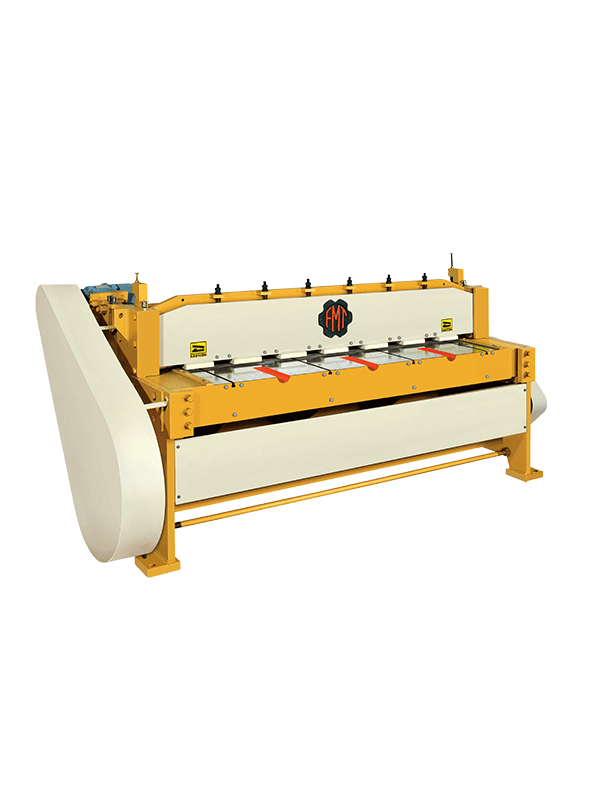
Under Crank Shearing
November 10, 2021Sheet metal cutting shearing
Cutting cycles are those wherein a piece of sheet metal is isolated by applying a worthwhile enough force to make the material fail. The most widely common cutting cycles are performed by applying a shearing force and are hence once in a while alluded to as shearing processes. At the point when an extraordinary enough shearing force is applied, the shear pressure in the material will exceed a definitive shear strength and the material will break down and separate at the cut area. This shearing force is applied by two apparatuses, one above and one underneath the sheet.
Regardless of whether these apparatuses are a punch and die or upper and lower sharp edges, the device over the sheet conveys a speedy descending hit to the sheet metal that rests over the lower instrument. A small clearance is available between the edges of the upper and lower instruments, which works with the crack of the material. The size of this freedom is regularly 3-10% of the material thickness and relies on a few components, for example, the particular shearing process cycle, material, and sheet thickness.
The impacts of shearing on the material change as the cut advances and are noticeable on the edge of the sheared material. At the point when the punch or sharp edge impacts the sheet, the freedom between the apparatuses permits the sheet to plastically twist and “rollover” the edge. As the device enters the sheet further, the shearing brings about an upward shined zone of material. At last, the shear pressure is too incredible and the material breaks at a point with a little burr framed at the edge. The height of every one of these bits of the cut relies upon a few components, including the sharpness of the instruments and the freedom between the apparatuses. Explore Pneumatic Power Press
Sheared edge
An assortment of cutting cycles that use shearing force exists to separate or eliminate material from a piece of sheet stock in various ways. Each interaction is fit for shaping a particular kind of cut, some with an open way to isolate a piece of material and some with a shut way to pattern and eliminate that material. By utilizing a large number of these cycles together, sheet metal parts can be created with patterns and profiles of any 2D math. Such cutting cycles incorporate the accompanying.
Shearing
As referenced above, a few cutting cycles exist that use shearing power to cut sheet metal. Nonetheless, the expression “shearing” without anyone else alludes to a particular cutting cycle that produces straight line slices to isolate a piece of sheet metal. Most normally, shearing is utilized to slice a sheet corresponding to a current edge which is held square, yet calculated cuts can be made also. Consequently, shearing is essentially used to cut sheet stock into more modest sizes in anticipation of different cycles.
Read about: What is Press Brake? How does the press brake work?
The shearing system
The shearing system is performed on a shear machine, frequently called a squaring shear or force shear, that can be worked physically (manually or foot) or by hydraulic, pneumatic, or electric power. An average shear machine incorporates a table with help arms to hold the sheet, stops or advisers for securing the sheet, upper and lower straight-edge edges, and a checking gadget to definitively situate the sheet. The sheet is put between the upper and lower edge, which are then constrained together against the sheet, cutting the material. In many gadgets, the lower cutting edge stays fixed while the upper edge is constrained descending.
The upper cutting edge is marginally counterbalanced from the lower sharp edge, around 5-10% of the sheet thickness. Likewise, the upper sharp edge is generally calculated with the goal that the cut advances from one finish to the next, in this way diminishing the necessary power. The cutting edges utilized in these machines ordinarily have a square edge as opposed to a blade edge and are accessible in various materials, for example, low amalgam steel and high-carbon steel.