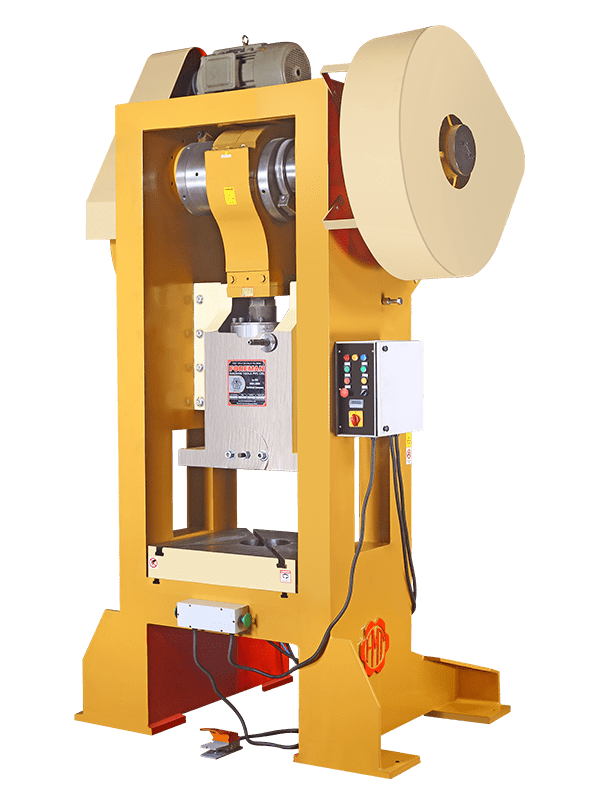
How Pneumatic Press is Utilized in Production, Manufacturing
November 29, 2021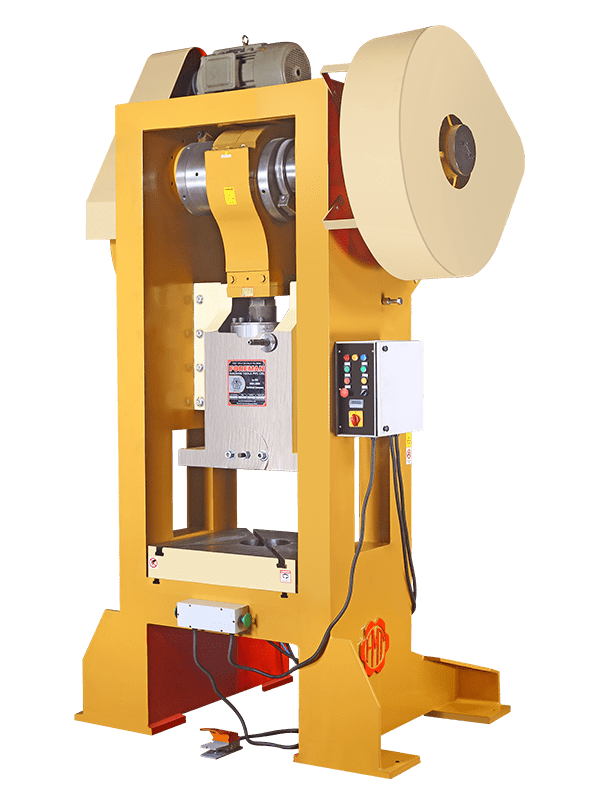
Pneumatic versus Hydraulic Systems: What is the Difference?
December 6, 2021Press Brakes
Press brakes are a requirement to nearest any metal manufacturing shop. Regardless of being one of the most significant and wanted pieces of machinery in a shop, they’re still miscommunicated, even by experts.
What Are Press Brakes?
Press brakes are machines that shape the sheet metal length. These metal sheets are commonly utilized in manufacturing and applications industries, or as parts for different gadgets. Most press brakes are evaluated by their ability to press metal and their general bending length; this is expressed in numbers. They come in many shapes and sometimes are furnished with tooling and additional items intended to make exceptionally customized parts. Press brakes fall into two major classifications: mechanical and hydraulic. In the next section, we’ll separate the difference and clarify the elements of each style.
Mechanical Press Brakes
Mechanical press brakes handle through an engine inside the gadget. This engine turns a wide flywheel at high velocities. The machine administrator manages the flywheel via a clutch, which then establishes the remaining parts into movement to twist the metal. The mechanical press brake is much more clear, particularly in regards to its gadgets, making management and tasks or processes simple. They can also deal with tonnages two to three times greater than their innate rating, because of the system’s mechanism. The essential drawback of utilizing mechanical press brakes is that the ram inside the machine should finish a full cycle when engaged and can’t be switched. This raises some security concerns if the machine operator commits a mistake and sets a few limits on the machine. One possible danger is the potential for the press brake to become locked if the ram travels too far. Explore Pneumatic Press Brake
Hydraulic Press Brakes
Hydraulic press brakes apply pressure by hydraulics to constrain the ram down, rather than depending entirely on mechanics. They might have more than one chamber and give the machine operator more exact command over the bend. The outcome is an exceptionally precise and adjustable bend. Like mechanical press brakes, hydraulics press brakes do have some particular drawbacks. Fundamentally, they can’t surpass the scope of their evaluated tonnage. Assuming your task requires adaptability, mechanical press brakes might be suggested.
Read more about: How Pneumatic Press is Utilized in Production, Manufacturing
Various types of Bending
There are two different ways press brakes can twist metal. The first is known as bottom bending because the ram will press the metal to the lower part of the die. Bottom bending outcomes in profoundly exact bends and depends less on the press brake machine itself. The drawback is each instrument is made to make one particular bend, so you’ll have to buy another one for each point you need to make. Air bending leaves an air pocket between the ram and the lower part of the die. This permits the administrator to contain for any spring back the material may give.
These kinds of die possibly should be modified if the material’s thickness is excessive. Air bending’s downside is the exactness of the point is impacted by the material’s thickness, so the ram should be changed out appropriately.